dead-weight testers, an introduction
Principle
Dead-weight Testers, also known as Pressure Balances, are named so because they utilize dead weights in determination of pressures operating in a closed and compressed system. For each value of the pressure applied, a predetermined mass (weight) is used to exert the force on fixed area (of the piston) to counter balance the buoyancy force.
The Dead-Weight Tester primary pressure standards that works on the basic principle of Pascal’s law, which is defined as “A change in pressure at any point in an enclosed fluid at rest is transmitted undiminished to all points in the fluid.”
The pressure ‘P’ in dead-weight tester is defined by the pressure definition:
P = mg / A
Where ‘m’ is the mass acting on piston area, ‘g’ is gravity and ‘A’ is the effective area of the piston
Units: SI unit for Pressure is Pascal (Pa), 1 atmosphere = 101325 Pa
Since ‘Pa’ is too small & inconvenient to use, we usually use other units for example: bar, lb/in² (psi), kPa, MPa, Kg/cm², in Water, mm Water, Hg Water etc.
Operating Range
The lowest pressure at which a pressure balance will operate properly varies between about 2% and 20% of its maximum pressure. It is sometimes claimed (and some certificates of calibration imply) that they can be used at pressures as low as dictated by the mass of the piston alone. This is not correct. Even if a piston appears to spin freely, it will produce results whose uncertainties will be difficult to calculate properly. The minimum pressures at which creditable performance is likely to be assured can only be determined by calibration
Operating Media
For hydraulic operation, the choice of the pressure fluid is a compromise between the demands of the system, for example low viscosity for fast response and minimal slowing of piston rotation, but without causing too much fluid to leak past the piston. The fluid should be compatible with all the components in the system and its electrical conductivity should be considered when, for example, calibrating piezo-electric devices.
Gas-operated pressure balances are normally used with filtered air or oxygen-free nitrogen, the latter normally providing the most trouble-free operation. The gas supply needs to be regulated at a pressure slightly in excess of the maximum pressure. For low gauge-pressure and below atmospheric (vacuum) operation a hand pump may be used. However for pressures below atmospheric a rotary vacuum pump is preferred.
Instruments to be calibrated against a dead-weight tester may have been used previously with a different pressure medium, remnants of which could contaminate the tester, and it is wise to take appropriate precautions. This might be to clean the test instrument, or to use a suitable separator (Oil Seal) which keeps the pressure media apart whilst allowing transmission of pressure across a barrier. Below pressures of about 0.3 MPa, where hydraulically-operated dead-weight testers accuracy is not so good, separators (oil seal) can allow hydraulics instruments to be calibrated against gas-operated testers. It should be noted, though, that all such techniques increase measurement uncertainties.
Hardware
Dead Weight Testers comprise mainly of three parts namely Testers Base, Masses (weights) and Piston Cylinder Unit. The Tester Base generates and regulates pressure (if it is oil operated), Masses apply force (F) on Piston Area (A).
Each weight is marked with the piston Serial number, piston area(s), weight set serial number and pressure equivalent. The total pressure measured is the sum of the weights plus the mass of the piston weight carrier when placed on a correctly floating and spinning Piston. Most of the Budenberg testers have a basic 10 lb/in² start, for other pressure units a makeup weight is added to the weight carrier for conversion to 1 bar (or kg/cm² or 100 kPa).
Certification and Environmental Corrections
All Dead-weight Testers are calibrated to the Gravity, Temperature and Air Density stated on the Certificate. The pressure equations and factors are given on the Certificate to adjust for any variations in these environmental conditions. Accuracy Software is supplied by Budenberg to make these correction if tester is supplied with UKAS accredited certificate.
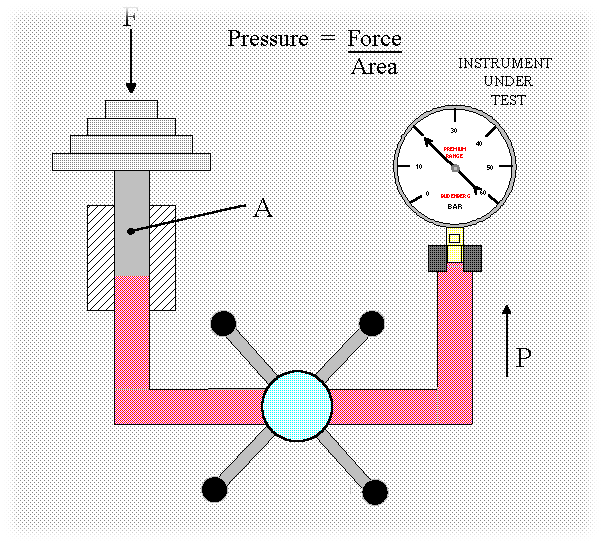
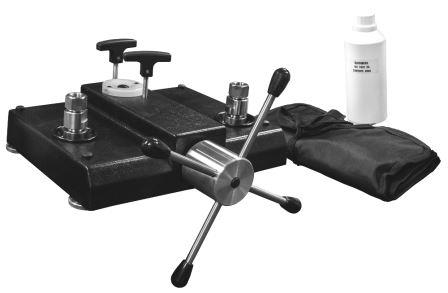
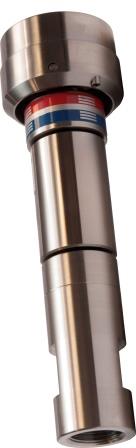
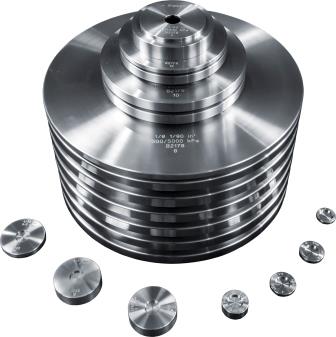
Acceleration due to Gravity
The value of Gravity varies greatly across the earth’s surface (0.5% due to latitude, plus 0.003% per 100 metre altitude) with geographic location. The variation, therefore, has a very significant effect on the downward force that each mass provides and so will the Dead-weight Tester reading. Dead-weight testers are usually calibrated at 980.665 cm/s², an international Standard Gravity. Hence, user should ensure that the Tester has either been manufactured to their local gravity or gravity correction is applied from the calibrated gravity.
Local Gravity Correction
If accuracy software is not available and local (site) gravity is known, the following calculation should be followed for applying local gravity correction on each reading.
Dead-weight Tester calibrated gravity as specified on the Calibration Certificate: 980.665 cm/s²
Assuming Local Gravity at site: 981 .565 cm/s²
Pressure measured (indicated): 100 bar
Actual or True Pressure
= (981.565 ÷ 980.665) x 100
= 1.00091774 x 100
= 100.09 bar
Temperature and Air Density Correction
These are less significant than Gravity. However, variations should be corrected for achieving maximum accuracy. In laboratories where the room temperature is controlled it is most likely that the temperature of the working parts of the unit will not differ from the ambient temperature by more than 0.5° C. When working in uncontrolled temperatures, however, one would have to measure the temperature of the piston unit.
Dead-weight Tester calibrated temperature (as on Calibration Certificate): 20°C
Operating temperature at site: 24°C
Percentage change /°C 0.002%
Pressure measured (Indicated): 100 bar
Actual or True Pressure
= 100 + ((20 – 24) x (0.002))÷100 x 100
= 100 – (0.008÷100) x 100
= 100-0.009
= 99.001 bar
Datum Levels
When testing gauges on liquid it is occasionally necessary to take into account heads of liquid since a height difference of 10 mm corresponds to approximately 1 mbar. The datum levels are marked on the outer diameter of the Piston Units. All Budenberg Pistons have datum levels marked. BGH120PCU, BGH700PCU, BGH1200PCU and BGH1400PCU units are marked with a groove on the outer diameter of the piston unit. The datum level of the model BGH300PCU is at the bottom of the knurled portion of the stud fitted to the unit.
Draughts
Dead-weight Testers are susceptible to draughts, even from seemingly gentle air-conditioning systems and should be screened to minimize such effects. A useful test is to switch air-conditioning fans off and on during the final stages of measurement to see if an effect can be detected.
Temperature and Humidity
Most Dead-weight Testers have piston-cylinder units made of steel and/or tungsten carbide and their areas change by between about 9 to 27 parts per million per degree Celsius. For high quality measurements it is thus important to measure the temperature of the piston-cylinder in order to apply a temperature correction.
It is not possible, however, to measure the temperature of a floating piston directly so it has to be inferred from the temperature of surrounding components. If the temperature of the room is not stable, the difference between the temperature of the surrounding components and the piston could be considerable and has to be estimated in calculating measurement uncertainties. Thermographs (recording thermometers are often used to monitor room temperature but it should be noted that they can have very long time constants and hence tend to indicate stable temperatures in the presence of significant short-term temperature fluctuations that affect pressure-balance operation.
The proximity of electric motors, for automatic piston rotation for example, can exacerbate temperature measurement problems, as can the presence of direct sunlight.
Air temperature and humidity (as well as atmospheric pressure) alter the density of air and hence the buoyancy effect it exerts on the masses. This in turn affects the resultant downward force on a pressure-balance and a correction has to be applied in the more demanding applications. If the air is very humid it may be necessary to protect some exposed parts to prevent rusting.
Vibration and Verticality
Vibration can have a detrimental effect on the performance of a Dead-weight Tester if it is sufficient to cause oscillations of the masses, in any plane, the result in a ripple or noise signal superimposed on the pressure being generated. Equipment should thus be mounted on firmly located solid benches that do not bend significantly in normal use, including adding and removing masses. In some circumstances it may be necessary to employ vibration isolation to a bench but it is important that it does not introduce significant tilt.
The axis of a Dead-weight Tester should be made vertical. This ensures that the force exerted on the pressure fluid by the mass of the piston and masses is maximized. Any departure from vertical varies and lessens the force and hence the pressure generated by a particular piston-cylinder and mass combination. For pistons with a rigidly attached weight-platform, a suitably sensitive spirit level should be used to adjust the alignment of the instrument. If adjustment ensures that the spirit level indication remains unchanged at several rotational positions of the piston, it can be assumed that the piston’s axis is perpendicular to ‘level’.
For other designs – for example those with an overhanging ring-weight carrier without a rigid platform – this may not be possible. In this case, levelling may have to be with respect to the top of the cylinder although the accuracy of this technique will depend on the perpendicularity of the top of the cylinder relative to its bore. For the most accurate work the non-verticality should be no more than about 2 arc-minutes.
Piston Cylinder Unit
As the piston/cylinder unit represents a high proportion of the total value of the tester. To ensure accuracy is maintained, it should always be handled with care and every effort made to keep it clean. The Tester is accurate when the weights are spinning and floating. When the piston is maintained well and tester is correctly set up and there are no leaks the piston head should “float” for many minutes.
Cleanliness
Cleanliness of a piston-cylinder assembly is particularly important and, to avoid contamination from skin acid, internal surfaces should not be touched directly. A number cleaning techniques are employed reference should be made to manufacturer’s instructions.
Methods for cleaning gas-operated assemblies generally involve solvent cleaning, polishing with a tissue and blowing the surface dry with dry filtered gas to remove particles. It is important to use solvents that do not leave a residue. Assemblies with smaller clearances sometimes benefit from cleaning with pure toilet soap and a hot water rinse; it is assumed that soap residue acts as a boundary layer lubricant.
If not thoroughly clean, the angular deceleration of a gas-operated pressure-balance will be noticeably higher, particularly at low pressures where momentum is less. It will also be less sensitive to small pressure changes (eg the addition of small weights) and might squeak. Under no circumstances should use of such a device continue without first cleaning it; permanent damage or change or change in effective area may result. After cleaning, pistons and cylinders should be given adequate time to reach a common temperature before re-assembly is attempted.
Oil Dead-weight Testers are less susceptible to dirt-induced problems and solvent cleaning is only necessary in extreme cases. The components should always be re-oiled before assembly, use or storage. Masses should be handled with care and kept clean. Any oil, dirt, corrosion or other damage will affect their mass values and hence the overall accuracy of pressures generated. They should be housed under a dust cover or in a storage box.
Fluid systems should be checked periodically for a foreign matter which could damage a piston-cylinder. Filters can minimise the risk of damage but they must be fitted where they cannot cause pressure differentials.
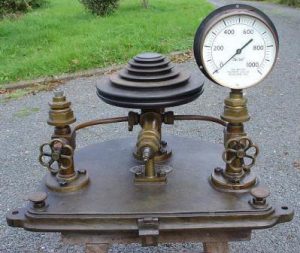
Budenberg Dead-Weight Testers
Budenberg has manufactured Calibration instruments for more than 100 years. Budenberg PRESSURE BALANCES (DEAD-WEIGHT TESTERS) and High Precision Pressure Test Gauges are symbols of first class Primary Pressure Calibration for calibration laboratories worldwide.
For those 100 years, Budenberg Gauge Company has been the leading manufacturer of precision Dead-Weight Pressure Testers enjoying worldwide reputation of superior accuracy, high quality, stability and robustness.
Budenberg’s latest BGH (Hydraulic) & BGP (Pneumatic) series inherits these qualities to which it combines excellent ergonomics and ease of operation. These are genuine primary standards which guarantee fast and reliable pressure calibrations on a daily basis and are specifically designed for workshop and laboratory.
Budenberg range of Dead-Weight Pressure Standards is available in Pneumatic and Hydraulic ranges which extends from -1 to 120 bar (1600 lb/in²) on air to 4000 bar (60,000 lb/in²) on oil with standard warranty periods up to 3 years.